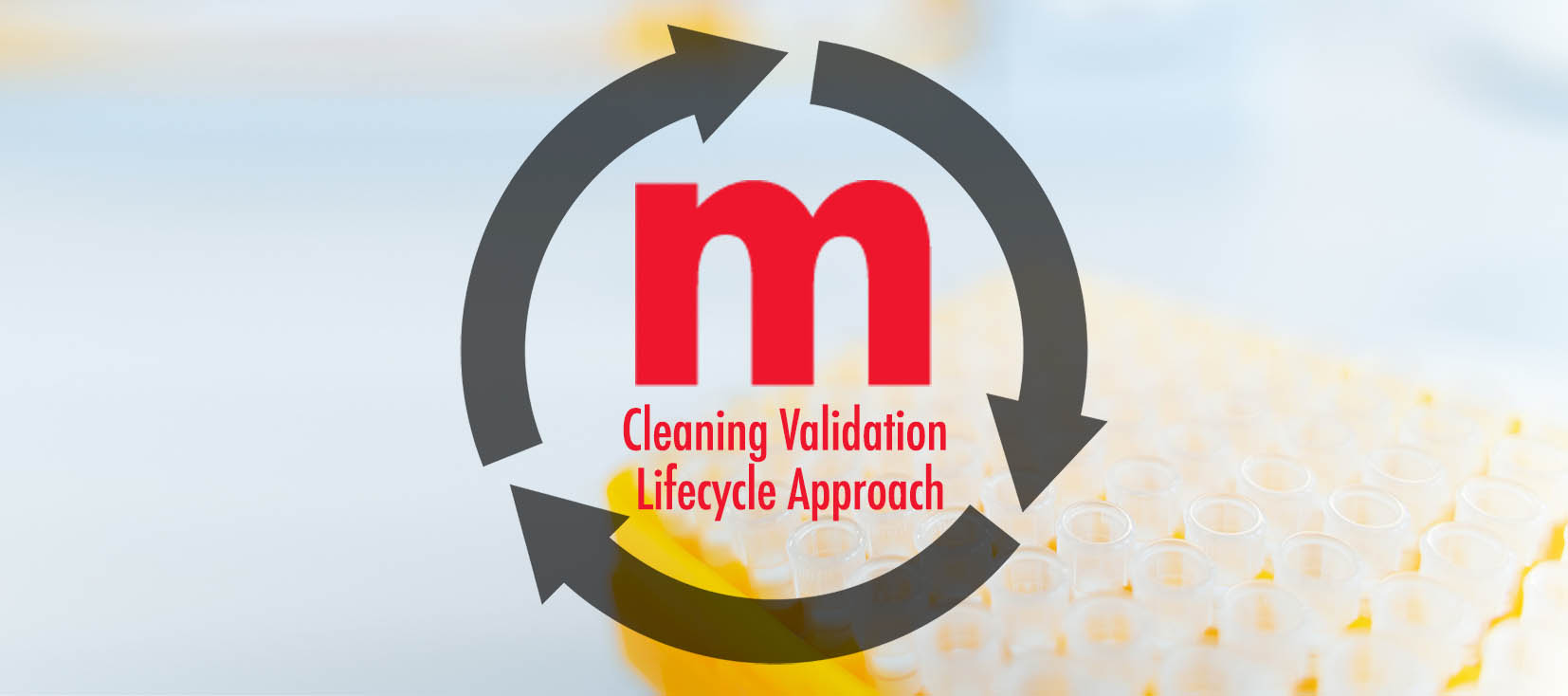
Cleaning Validation Lifecycle Approach
Nel 2011 FDA ha pubblicato una guida sulla convalida di processo (Process Validation: General Principles and Practices), concentrandosi su tre principi fondamentali:
- La qualità non è garantita da test in corso o finali;
- La qualità deve essere integrata nel processo;
- Il processo di produzione deve essere definito e costantemente monitorato per garantire una qualità costante.
L’approccio al processo descritto dal modello Lifecycle (ciclo di vita), come presentato nel documento, si concentra sulla comprensione dei processi e sulla garanzia che soddisfino i requisiti stabiliti in fase di progettazione. I principi descritti non devono essere limitati alla produzione poiché possono essere applicati anche ad altri processi, compresa la pulizia.
Gli elementi dell’approccio Lifecycle sono la base costitutiva di una gestione armonizzata della convalida di processo e di pulizia, in un contesto di produzione in batch e in continuous manufacturing. Questi elementi possono essere riassunti in: 1) design e progettazione, 2) convalida e 3) monitoraggio continuo. Tenendo presente questo, il modello Lifecycle può essere utilizzato per migliorare o ottimizzare le procedure di pulizia grazie a una migliore comprensione delle variabili di input e degli attributi di output.
Design e progettazione
La fase di progettazione è di particolare importanza perché il processo di pulizia è definito sulla base delle conoscenze acquisite attraverso le attività di sviluppo e di scale-up. Abbiamo già visto alcuni aspetti di design di processo ed equipment di pulizia in un nostro precedente articolo. Qui ricordiamo che è necessaria una valutazione formale del rischio utilizzando gli strumenti descritti in ICH Q9, quali Fault Tree Analysis (FTA), Hazard Analysis and Critical Control Point (HACCP), Failure Modes and Effect Analysis (FMEA).
Un approccio DOE (Desing of Experiment) può essere utilizzato per identificare quali parametri hanno un impatto significativo sulla pulizia e il loro intervallo di variabilità, garantisce l’identificazione delle variabili e la valutazione della loro criticità per il processo di pulizia. Ad esempio, gli input da considerare per la fase di lavaggio possono includere: l’agente di pulizia, la concentrazione, la temperatura, il tempo, il metodo di pulizia, la qualità dell’acqua e altri fattori ambientali. Dovrebbero essere utilizzati studi di laboratorio, studi pilota e sul campo per aiutare a definire le condizioni che portano al risultato desiderato, in modo veloce, efficace e snello (lean).
Convalida
Il primo step della fase convalida cleaning è la determinazione dei livelli residui di prodotto. Se come esempio prendiamo una linea monoprodotto (o continuous manufacturing) si possono presentare due casi:
- La produzione del prodotto A viene interrotta a causa di un evento di manutenzione o di una pulizia minore come l’aspirazione o pulizia a secco delle superfici (l’evento può essere programmato o non programmato);
- La produzione del Prodotto A viene interrotta e si inizia la produzione in continuo del Prodotto B.
Per quanto riguarda il caso 1) la cleaning validation non è applicabile in quanto non c’è rischio di cross-contaminazione di principio attivo perché la linea è monoprodotto. Tuttavia se vengono usati detergenti o lubrificanti particolari un processo di cleaning deve essere effettuato per l’eliminazione dei residui.
Nel caso 2) è sempre necessario effettuare una pulizia completa e accurata di tutta la linea per assicurare che i componenti del prodotto A, insieme agli altri agenti impiegati (detergenti, ecc.) e residui microbici, non abbiano effetti sulla qualità del prodotto B. Sia nella produzione in batch che in continuo dobbiamo poter escludere qualsiasi effetto farmacologico e tossicologico del prodotto A sul prodotto B, stabilendo dei limiti massimi consentiti per le sostanze coinvolte.
Per la definizione del limite massimo consentito (L1) è necessario l’utilizzo di equazioni e calcoli, diversi caso per caso, che coinvolgono parametri scientifici, quali Acceptable Daily Exposure (ADE) o Permitted Daily Exposure (PDE), safety dose (L0), Maximum Allowable Carry-Over value (MAC o MACO), e di processo, quali batch size e superfici interne dell’equipment. Dividendo L2 o MAC per la superfice totale in contatto con il prodotto otteniamo il limite per unità di superfice, supponendo una distribuzione uniforme del residuo sulla superfice stessa.
La distribuzione uniforme viene considerato come ipotesi conservativa e si riferisce ad una situazione ideale che non è quasi mai vera in pratica. Questa assunzione potrebbe portare a risultati sbagliati nella selezione dell’equipment e dei punti di campionamento. In molti casi reali ci si rifà all’approccio non uniforme o stratificato del residuo: in questo caso il piano di campionamento (swab sampling) prevede di campionare solo i punti più difficili da pulire, come worst-case, individuati tramite analisi del rischio. Ovviamente è molto importante documentare l’analisi nel modo più corretto e completo possibile perché questa sarà il punto centrale della convalida e sarà revisionata dagli ispettori.
Il passo finale è la qualifica delle performance (PQ), che nell’approccio Lifecycle è costituita da varie verifiche atte ad assicurare che la procedura di cleaning sia pronta ad entrare in uso: SOP e WI revisionate ed approvate, training completo del personale addetto, qualifica dei fornitori, metodi analitici convalidati, equipment di processo e utilities sono qualificati. Se i parametri critici di processo (CPP) e gli attributi critici di qualità (CQA) sono stati ben caratterizzati durante la fase di design e progettazione, la fase di PQ non rappresenta un particolare sforzo per la convalida.
Si conclude questo breve excursus su alcuni degli aspetti di design e di convalida; in un prossimo articolo dedicato alla Cleaning Validation affronteremo il terzo e ultimo aspetto, ovvero quello del Monitoraggio Continuo.
FORMAZIONE
Process And Cleaning Validation
*Corso disponibile anche in modalità in-house: data da concordare con l’azienda
Tag
Share
STAY IN THE LOOP
Iscriviti alla nostra newsletter.
[mailup_form]
SAP S/4 HANA: come cambia l’approccio alla convalida SAP ERP (Enterprise Resource Planning), fin dalla sua iniziale concezione ormai risalente […]
Implementare la nuova release di SAP, denominata S/4 HANA, è ormai un must per tutte le aziende che usano già […]
Sistema Qualità. Se la tua azienda subisse un controllo oggi, ti sentiresti davvero al sicuro? La qualità è cruciale nell’industria […]
Il Cliente e le Sue necessità Evotec SE è una società di drug discovery and development quotata in borsa con […]